■企業紹介 - 有限会社小川製作所
★ 会社概要
- 企業名:有限会社小川製作所
- 創 業:昭和40年(1965年)2月
- 所在地:岡山県総社市総社赤浜600(テクノパーク総社内)
- 事業内容:
- 各種専用機・治具等の設計・製作
- 保守・メンテナンス
- 製缶、機械加工、電気設計
- 三次元測定サービス
- 電力測定サービス

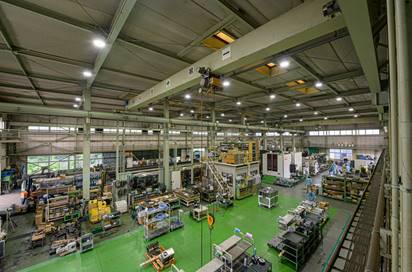
当社は、岡山県内外の製造業や工程における生産性向上と課題解決を行うためのオーダーメイドの自動化設備や治具の設計・製作を行う生産システムインテグレータです。お客様の「想い」をカタチにすることを使命とし、綿密なコミュニケーションを通じて真のニーズを引き出し、性能、コスト、作業性を考慮した最適な設計を心掛けています。 |
|
●DX導入の背景ときっかけ |
|
今回のIoT伴走支援事業に取り組むきっかけは、(一社)システムエンジニアリング岡山(以下、SEO)のチラシとの出会いでした。以前より社長から後継者である私に、何か取り組むテーマを見つけるようにという指示があり、製造業の分野でDXを活かせることはないかと探していました。そのような状況の時に、「IoT伴走支援事業で専門家のアドバイスを受けられる」と書かれたチラシを目にし、システムエンジニアとしてのキャリアを持つ私にぴったりだと思い応募しました。 この事業に応募する時点での課題は、在庫管理の効率化を目指した取り組みであり、設備製造に必要な鋼材や購入部品、工具類などの資材在庫を適切に把握し、管理や作業の無駄を省くことでした。しかし、伴走支援で派遣されるITコンサルタントとの議論を通じて、業務プロセスの改善や5S(整理・整頓・清掃・清潔・躾)、さらには資材在庫の量に基づくABC分析などの情報提供を受け、業務そのものの改善とデジタル化による改善の両方が必要であり、業務改善を行いました。また、デジタル化に取り組むためには在庫管理の業務やデータの流れを把握する等の事前準備が必要な事が分かりました。 その後、プロジェクトを進める中で、当社の顧客から「生産ラインにおける生産情報の見える化」に対するニーズが発生しました。このことに対し、生産システムインテグレータとして、単に顧客の仕様に基づく生産ラインの設計・製造だけではなく、保守・メンテナンスに加え、生産性向上の取り組みの支援など、デジタル化による課題解決が必要であると判断し、IoT技術を取り入れた顧客の生産ライン構築への取り組みを決めました。 当社は、過去にも製造業の顧客から同様の相談を受けていたため、このニーズに応える製品開発が実現できれば製品の新たなアドバンテージになると考えました。当事業のITコンサルタントに相談したところ、生産ラインの稼働状況等の数値の見える化に関する事例や進め方等の情報提供があり、実現可能性を検討することができました。その結果、社内にあるマシニングセンタを活用したIoT技術による稼働率等の生産情報の見える化の検証が容易であることから取組を決定しました。この取り組みにより、経営指標と生産管理指標を統合的に管理することが可能となり、製造工程全体の効率化にも取り組めることが明らかになるなど、目標が明確になったと感じています。 |
|
●取り組みの苦労と学び |
特に大変だったのは、RFI(情報提供依頼書)を初めて作成し、社外のデジタル化の協力会社であるITベンダーへの説明を行うことでした。このプロジェクトは、月に1回のミーティングを5か月間実施するもので、プロジェクトの完了に向け、ITコンサルタントが毎月決定すべき項目を設け、それに対する宿題をこなすことで進められました。しかし、その宿題の一つであるRFIを作成するのは初めてであり、特に、自社内では当たり前になっていることを社外の人にわかりやすく説明し、協力を依頼することが難しく感じました。この背景には、製造業のプロセスに関する専門知識の不足や、独自の文化に対する理解が不十分だったこともあったと思います。 |
その後、専門家による支援チームからRFIの作成方法やサンプルに関する情報提供を受け、アドバイスをもらいながら作成を進め、解決すべき課題やその要因、解決方法、ツールについてディスカッションを重ねながらまとめることができました。また、そのRFI作成を通じて情報共有が進み、SEOの会員企業80社の中から最も適切と思われるITベンダーとして、株式会社日伝 様を紹介して頂きました。このようにRFIを作成する機会がなければ、腰を据えて現状分析することがなかったと思います。 さらに、企業の後継者として、この過程で現場の従業員との意見交換を行い、IT導入に対する不安を払拭するための地道な努力を重ねたことで、信頼を得られるようになったと感じています。特に、工場内の業務プロセスを可視化し、関係者全員で課題を共有する姿勢をみせることができたのが重要な成功要因となりました。 成果物は業務フローチャートであり、この作成により支援活動を進める上で共通の理解を得ることができました。どのような流れで仕事を進め、どこでどのような情報が生まれているのかを可視化し、仕事への理解が深まりました。一方で、業務プロセスの中でブラックボックスとなっていた部分もあり、工場長や社長とのコミュニケーションを通じてその詳細を明らかにすることができました。このような機会が少なかったため、無策で話しかけても社員の協力は得られないことを実感しましたが、フローチャートを作成から、「ここを教えて欲しい」という具体的な課題が見えてきました。 |
|
●具体的な施策と成果 | |
今回のプロジェクトを進める中で、次の施策を実施し、以下の成果を得ました。
○IoTネットワーク環境の整備 自社工場内にメッシュWi-Fiを導入し、各設備やセンサーがスムーズに連携できる環境を構築しました。これにより、マシニングセンタの稼働率をリアルタイムで把握できるようになり、収集した稼働率データを活用した改善活動により生産効率が向上しました。 ○在庫管理の見える化 専用ソフトウェアとハードウェアを導入し、鋼材の在庫データを一元管理しました。これにより、在庫過剰や欠品のリスクが低減し、材料コストの削減への意識が高まっています。 ○生産情報の見える化による設備導入パッケージの開発 自社工場におけるIoTネットワークを活用し、マシニングセンタの稼働率の把握やセンシング技術を活用した鋼材の在庫データの一元管理がリアルタイムで可能となりました。この結果、顧客の設備導入時の生産情報見える化システムのPOC(概念実証)を開始することができました。 この社内での概念実証を通じて、マシニングセンタの稼働率を可視化するダッシュボードを開発しています。2024年1月に要件定義を行い、2月から8月にかけて開発と社内検証を実施しました。具体的には、マシニングセンタの稼働状況や鋼材の在庫状況を管理するシステムを構築することにより、リアルタイムな稼働状況や鋼材の量の把握など、一定の効果を得ました。その後、当システムの運用も開始され、これにより、生産・在庫データ処理等の事務的な工数削減が見込まれています。 これまでは、ISO14001の要求に応えるために、Excelを使用して稼働状況を管理していましたが、そのために毎月一定の事務作業が発生していました。この作業をIoT機器の導入により自動化することで、待機時間や稼働時間を効率よく把握できるようになり、機器の電源が入っている時間や故障時間も可視化されました。PLCと呼ばれるプログラム可能な論理回路の制御装置からデータを有線で取得し、CSVファイルを自動で生成。事務の手間を削減し、Excelでのグラフ作成も自動化しました。これにより、毎月3時間かかっていた作業がゼロになりました。 また、鋼材の在庫状況の見える化にも取り組みました。この結果、従来は設計者が在庫確認のため現場に足を運んでいましたが、事務所で確認できるように改善することで人の移動時間の削減を図りました。また、受発注システムからデータを取り込み、材料消費量をExcelから自動で吸い上げるプログラムを作成しました。これにより、無駄な鋼材の購入がなくなり、設計者が在庫のある鋼材を使って図面を作成するようになり、無駄な在庫を減らすことができました。 現在は、このIoT機器による生産情報の見える化への取り組みは、POC(概念実証)に向けて開発が進行中であり、社内の実績を活用し、今後は顧客への提案も行っていく予定です。実際、すでに1社がこの見える化の提案の依頼があり、NDAを結んでPOCを進める準備を整えています。今後、IoT機器による生産情報の見える化生産ラインのパッケージ化に取り組み、顧客ごとのニーズに合わせた提案を行っていきます。 |
|
●株式会社日伝による伴走支援 | |
今回の岡山県様のIoT等導入実践促進事業を通じて、解決すべき課題の定義を行った結果、IoTの専門ITベンダーである株式会社日伝様を紹介していただき、プロジェクト全体の計画策定から運用まで伴走支援を受けることができました。ITベンダーの紹介に際しては、ITベンダーの営業担当者だけでなく、日伝様のIoT専門アドバイザーも交えたミーティングを実施し、ネットワークやセンシング関連の豊富な機器類とその組み合わせによるシステムに関する情報を得ることができました。
さらに、当社の無線Wi-Fiに関する課題を抽出し、工場全体を電波でカバーできるメッシュWi-Finのアドバイスも得て導入しました。これにより、IoT化を進めるための強固なネットワーク環境が整備され、その結果、社内のITリテラシーが向上し、現場への新技術の浸透がスムーズに進みました。 日伝様との連携は社内のネットワーク環境整備をする上で非常に助かりました。RFIを出すことにより、これまで考えたことのなかったIoT関連機器類が使えることを教えていただき、そのおかげで具体化が進みました。もしそのような支援がなければ、プロジェクトの進行はここまでスムーズには進まなかったと思います。 一方で、社内での検証用にメッシュWi-Fiのアクセスポイントを購入して取り付けました。メッシュWi-Fiは、機器を網のように配置することで工場全体に電波を満たすことができ、従来のWi-Fiとの違いIoTに必要なネットワーク環境が整い、スムーズな運用が可能となりました。 |
|
●今後の展望 | |
現在の段階では、まだパッケージ化には至っていませんが、今後の展望としては、同じ目線で近いニーズを持つ顧客とのPOC(概念実証)を積極的に進め、パッケージ化の候補を見つけていきたいと考えています。当面は、顧客毎のニーズに応じた提案や開発を行い、実績を積み重ねることで、最終的なパッケージ化を目指していく方針です。
複数の製造業の企業と話す中で感じたのは、IoTやDXの取り組みではパッケージソフトだけでは解決できない課題が多いということです。特に中小製造業では、誰にも拾われないニーズや課題が多数存在し、それに伴走する形で支援していくことの重要性を強く認識するとともに、この事業に大きな期待を寄せています。 当社は元々、ロボットシステムインテグレータとして生産ラインのインテグレーションを担ってきました。この経験は、ITシステムのインテグレーションへとシフトしても、本質的には変わりません。中小製造業の人員削減や自動化に関する課題に対して提案する姿勢は変わらず、私自身のITスキルと経験が生かせる領域だと感じています。 現在の成果を土台に、ロボットシステムインテグレータとして設備を高度に活用する強みを育成し、さらなる発展を目指していきます。特にPOC(概念実証)を通じて、今回構築したシステムをパッケージ化し、他の中小製造業への展開を計画しています。この取り組みは、単なる生産効率向上だけでなく、日本全体の中小製造業の課題解決にもつながる可能性を秘めています。 また、将来的にはAIを活用した予測分析や、自律的な業務プロセスの構築にも挑戦したいと考えています。 |
|
●中小企業へのメッセージ |
|
1.小さな成功体験を積み重ねること 2.素早く取り組むこと 3.少人数での進行 4.味方に頼りすぎず、自ら動くこと 5.トレーサビリティの重要性 6.社長との関係性 7.若い人や熱意を持つ人の挑戦を応援する 8.DXを進めるためには継続的な挑戦が必要 |
|
●支援ベンダーの声 | |
◆ 株式会社日伝
弊社は、多様なモノづくりの現場でシステムコーディネートを行ってきた機械系商社です。製造業界での実績と専門知識を活かし、近年は企業の成長とDX変革のサポート事業にも注力し、デジタル技術を活用した生産性向上や品質管理強化に力を入れるとともに、オーダーメイドのソリューションを提供しています。 ★施策実現のポイント(支援において配慮したこと) 弊社は、DX化支援において密なコミュニケーションと柔軟なサポートを重視しております。たとえば、今回の小川製作所様に対するBR-400AN(メッシュWIFIアクセスポイント)の納入時には、環境に最適な運用を実現するため、事前に詳細な調査を行いました。また、PoC(概念実証)の過程で発生する可能性のある障害を防ぐため、定期的な情報交換を行い、進捗の確認や迅速な対応策の共有を徹底しております。 ★ベンダーとしての施策実現プロセス 今回は、以下の3ステップで中小企業のDX化支援を進めました。
★ベンダー視点での取組企業の成功ポイント 今回のDX化プロジェクト成功の鍵は、顧客企業の主体的な推進力と計画性の高さにあります。社内試験運用を徹底し、外部ヒアリングを積極的に活用した点や、提案内容への深い理解が、スムーズな移行を支える要因となっています。㈱日伝は、顧客の自主的な取り組みを最大限サポートし、信頼されるパートナーとして引き続きDX化成功に貢献してまいります。 |
|
■まとめ - 伴走支援で実現するDX
★ 本事例のポイント
- IoT環境を構築し、業務の「見える化」を実現
- 実証実験を通じて新しいビジネスの可能性を探求
- SEOの伴走支援により、スムーズなDX導入が可能に
★ これからDXを検討する企業へ
- DXはスモールスタートで始めるのが成功のカギ
- 業務の可視化が生産性向上につながる
- SEOの支援を活用すれば、専門家と共にDXを推進できる